The last few articles in this series have focused on utilities, including recovering expenses from tenants, improving operational efficiency, and avoiding the added costs of regulatory fines and purchasing renewable power.
With utilities, the value technology provides is linear. When an insight is implemented, small savings accrue daily, adding up to significant sums when annualized.
Conversely, in the world of repairs and property damage, value comes in large, one off events. Instead of saving $200 a day, a property might save $80,000 in an afternoon.
This makes adoption challenging for some portfolios. Humans naturally have a normalcy bias, which leads us to underestimate the likelihood of disasters.
And when looking at technology only through that lens, the return on investment of point solutions will either be 0% or 1,000% - something that’s not easy to model or invest in broadly.
The point of this series is to demonstrate how the value of technology compounds over time. Averting disaster naturally flows from improving productivity, consolidating technology, and deploying real-time monitoring. Avoiding property damage is critical to cash flows, but couldn’t have been the first step.
Embracing Preventative Maintenance
Preventative maintenance is like eating your veggies. Value comes from consistency. When you don’t do it, nothing bad happens… at first.
In one salient example, there is an Enertiv client that had chronic equipment issues. These caused tenants to complain and led to expensive repairs.
When asked, property teams explained that they were too busy dealing with tenant emergencies to follow the tedious preventative maintenance schedules.
After adopting technology (and frankly, going through some change management), time spent on preventative maintenance went up by 300%.
The results were immediate and dramatic. Within a month, there were 75% fewer tenant tickets. The property spent 25% less on repairs from outside vendors.
This pattern has been repeated across property types and management structures.
The data is clear. What’s also clear from experience is that this value only accrues when there is buy-in from the on-site team. That is why productivity was the first article in this series. Their lives have to be made easier first, then the direct value is realized, not the other way around.
Once a preventative maintenance program is being followed, there's an opportunity to increase efficiency.
For example, the same BMS and equipment monitoring mentioned previously for energy savings can also be used to calculate runtime hours.
Using that data, maintenance schedules can be optimized based on how much equipment is actually being used, rather than based on calendars and manufacturer’s assumptions.
The analogy is an odometer on a car. Oil changes and other upkeep could be done based on a calendar, but knowing exactly how many miles have been driven makes the maintenance much more precise.
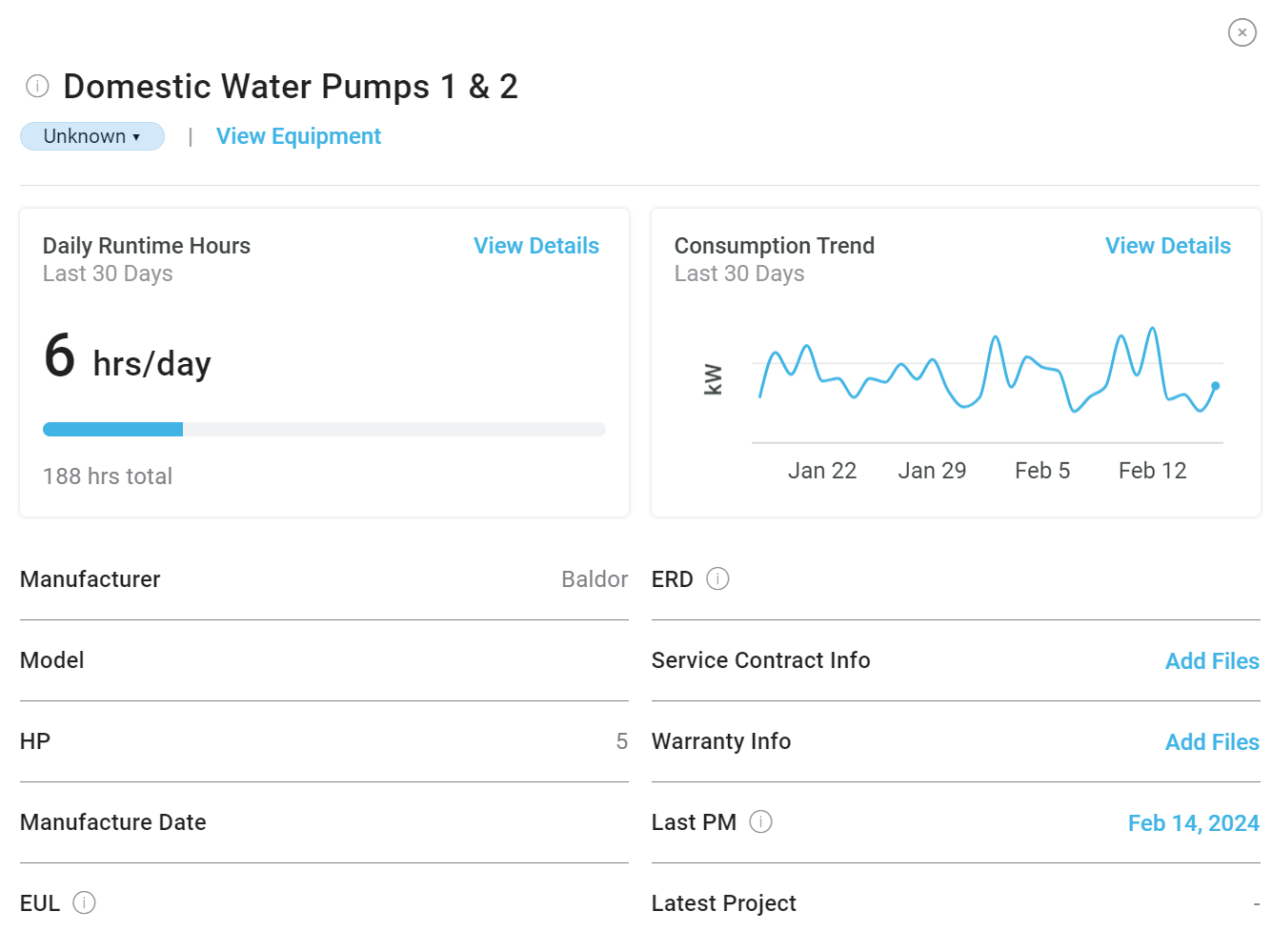
Detecting Equipment Faults
There is a famous stat that came out of the largest study on preventative maintenance in history (performed by the US armed forces).
It found that 82% of equipment failures occurred at random.
The insight being that even the best preventative maintenance program cannot eliminate the possibility of small issues going unnoticed until they become serious problems.
In addition to identifying energy insights and calculating runtime hours, real-time monitoring detects equipment issues the moment they occur.
Fault detection is not a new concept. What is novel is A) using machine learning to significantly reduce the “noise” of inconsequential faults, and B) connecting faults directly into work order ticketing (and preventative maintenance).
When combined with robust preventative maintenance, the results on repair costs can be dramatic.
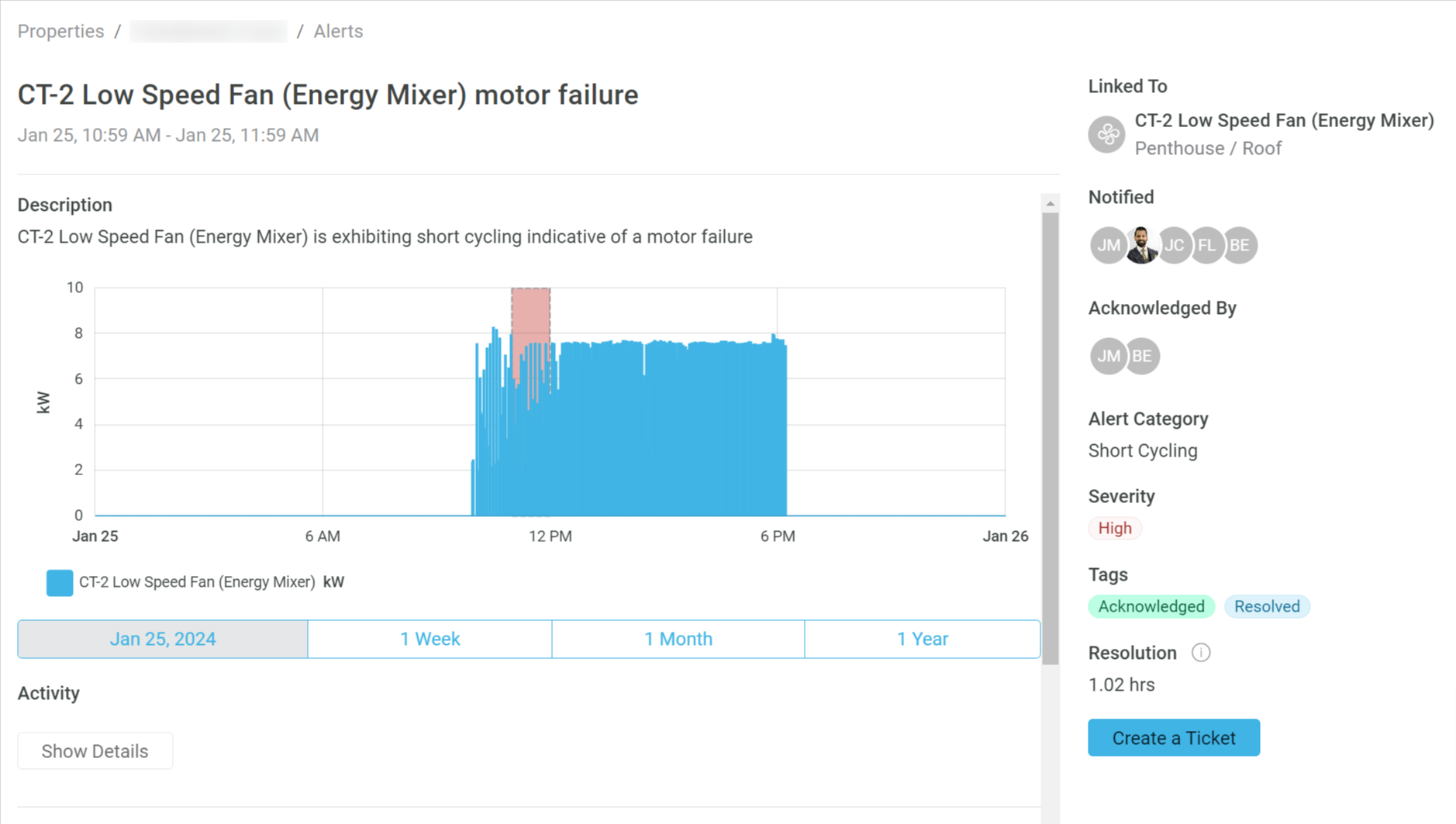
Preventing Water Damage
Of course, equipment repairs are just one of the sources of large, unexpected costs.
Water damage claims cost three times as much as a claim that does not involve water damage. And water damage claims account for more than half of all commercial real estate insurance claims.
The two most common strategies to mitigate these disaster scenarios with technology are with leak detection and temperature monitoring.
Leak detection is straightforward. The moment moisture is detected, whether from roofs, toilets, HVAC equipment, or in basements, alerts are sent.
Temperature monitoring is deployed primarily in regions that experience freezing temperatures during the winter. Every time there is a cold snap, portfolios lose weeks and tens of thousands of dollars dealing with the consequences of pipes freezing and bursting.
In this case, the goal is to alert operators before moisture is detected, by delivering an escalation of alerts as temperatures around plumbing infrastructure approach freezing.
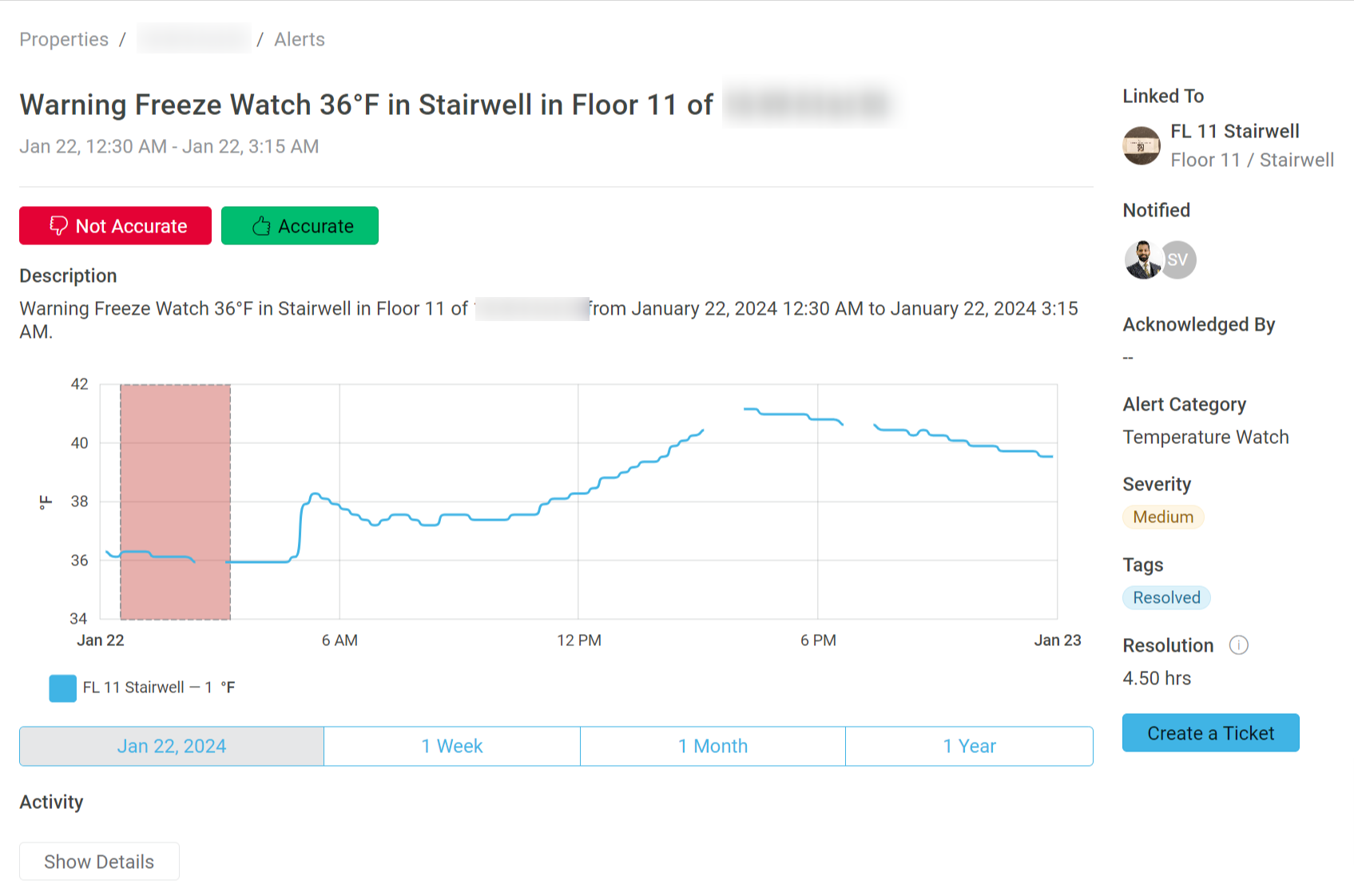
Conclusion
The right technology can almost eliminate the most common and expensive disaster scenarios in commercial real estate.
And yet, due to the tendency to discount the likelihood of major negative events, adopting technology for this explicit purpose remains a challenge.
That is why it is more effective to frame technology adoption as compounding value.
Preventative maintenance depends on operator buy in, which in turn depends on the value technology provides them in terms of increased productivity.
Likewise, fault detection is derived from real-time monitoring. Integrating with systems and deploying sensors is an investment. If that investment is paid for with energy savings, the benefits of reducing repairs and property damage are self evident.