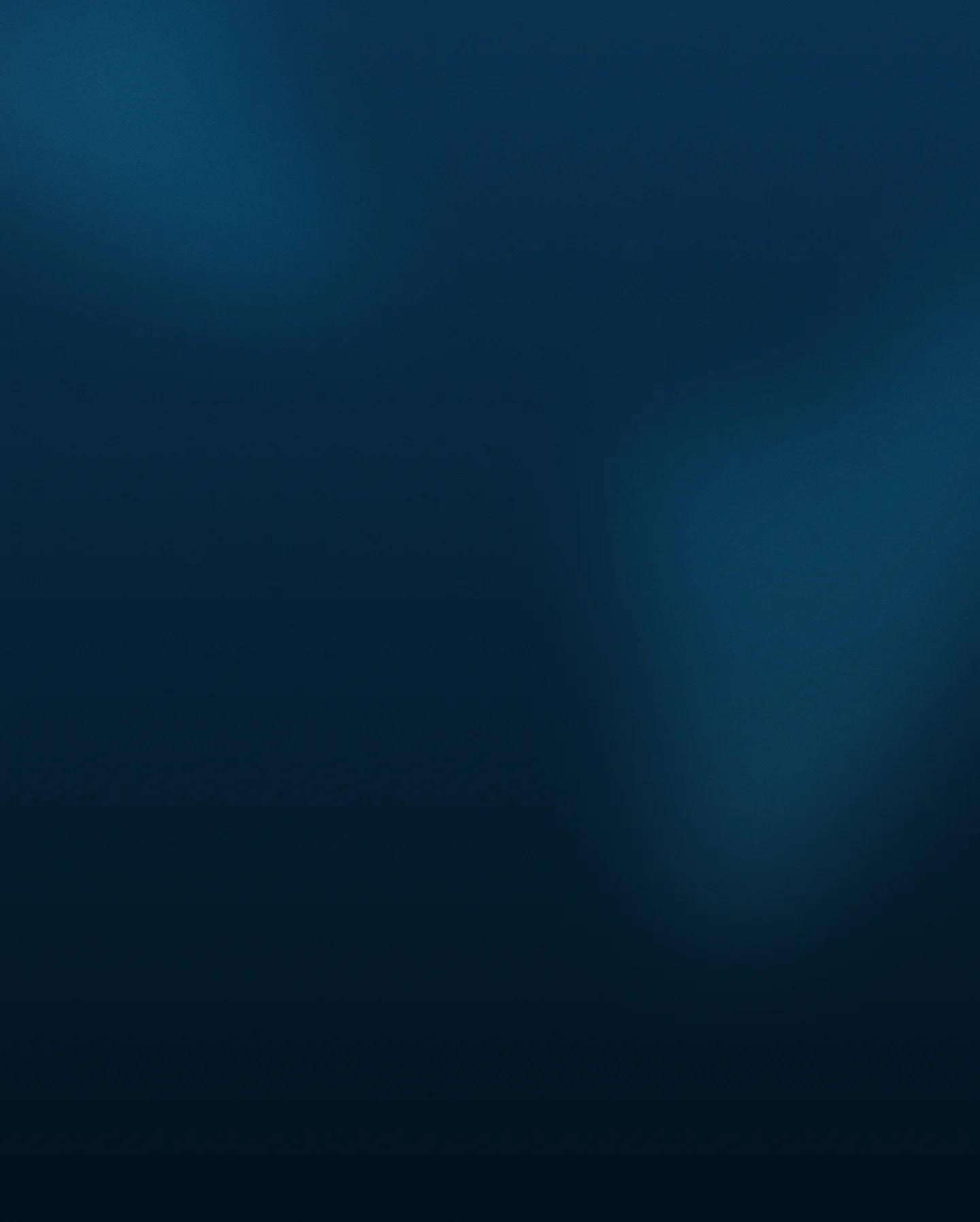
Stack Real Estate cuts operator onboarding time by 50% and saves $178,000 in HVAC costs
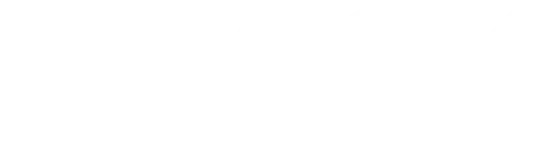
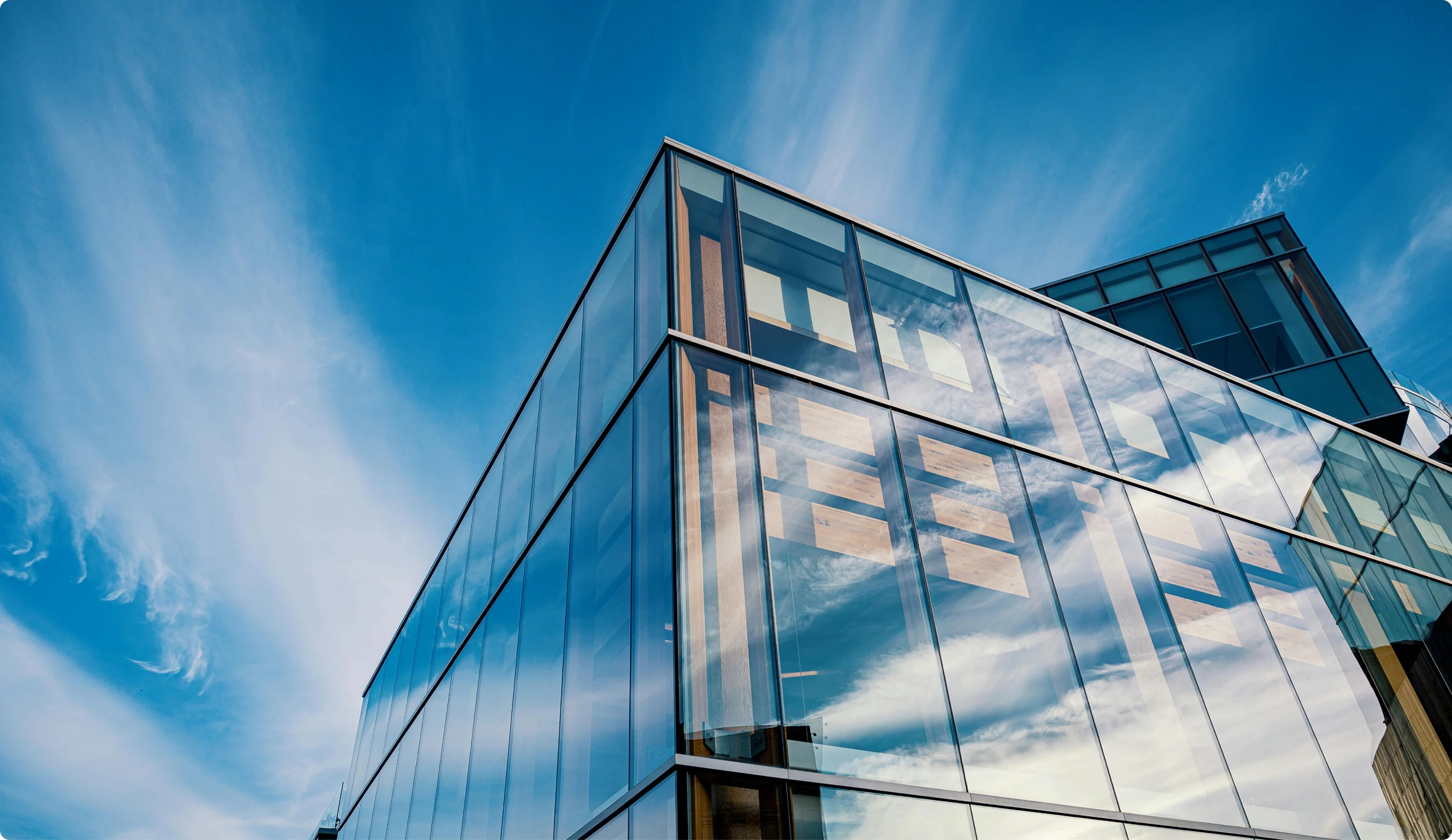
Challenge
Thanksgiving Station is a 1M sq ft Class A office campus in Lehi, Utah. As the expectations on the engineering team have increased, they have looked to technology to improve their productivity and the building’s efficiency.
This was made more difficult by turnover with the on-site teams.
Outcome
Stack Real Estate’s engineering team quickly adopted the Enertiv platform, both to manage their daily operations and to enhance performance. Within 6 months, the team had implemented savings amounting to $178,000 annually across the campus.
In addition, the facilities coordinator is looking to cut the onboarding time in half for new operators by leveraging the digitization of equipment inventories, documentation, and maintenance logs now all available in Enertiv.
Journey
STEP 1 - DIGITIZATION
As with every deployment, the Enertiv team started by digitizing the asset. This includes taking pictures of equipment, digitizing files such as warranties, service agreements and O&M manuals, and taking 360 scans of the mechanical rooms to enable remote access.
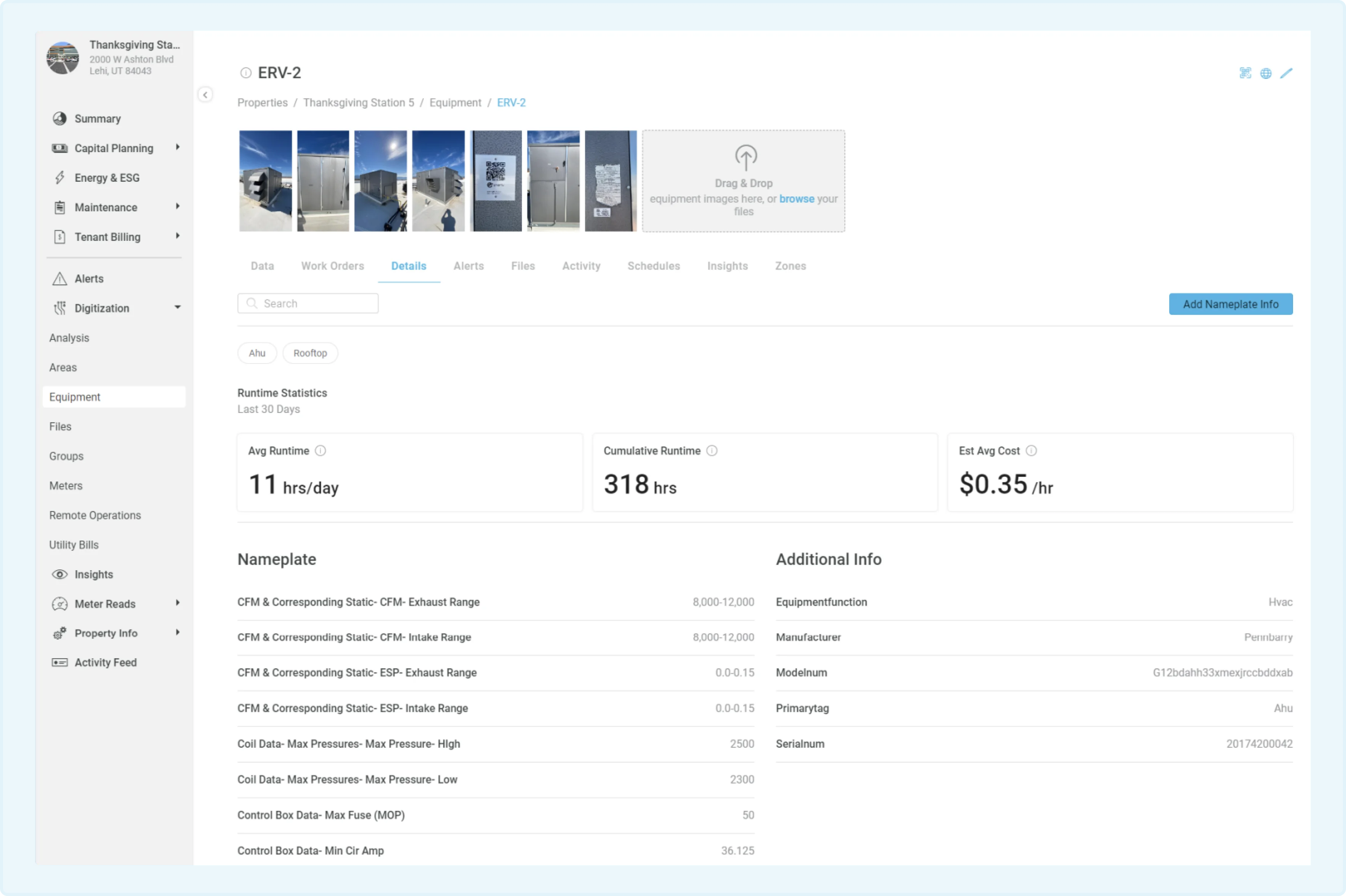
STEP 2 - MAINTENANCE
Next, Enertiv’s Client Success team transferred the existing rounds and preventative maintenance schedules in the Enertiv App. Where opportunities presented themselves, ASHRAE templates were pulled from Enertiv’s library to ensure best practices were being followed. In addition to the on-site team’s work order schedules, Enertiv has onboarded the asset’s third party maintenance provider. This has given the team the ability to hold vendors accountable in a way that was never possible before.
More recently, I went with one of the technicians to the roof of one of our buildings to do an inspection. We noticed that a belt was cracked and needed to be replaced and we logged it right there in the app. Going forward, there will always be a record of exactly which rooftop unit had its belt replaced, when and why.”
STEP 3 - REAL-TIME MONITORING
In the background, while the asset and workflows were being digitized, Enertiv had deployed equipment monitoring sensors and integrated with the BMS.
Once the data had been baselined, there was a final onboarding session to walk through the capabilities unlocked by real-time data.
The first new capability was alerts, automated notifications that are sent out based on Enertiv’s algorithms as well as custom alerts implemented for specific scenarios. In the first 6 months, the team received 67 alerts, and maintained an incredible Alert Score of 92/100, well above industry average.
The second new capability was insights, these are opportunities to improve operations and reduce curated by Enertiv’s Building Intelligence Engineers.
In total, the team has implemented $178,000 worth of savings, mostly by using data to fine tune HVAC schedules
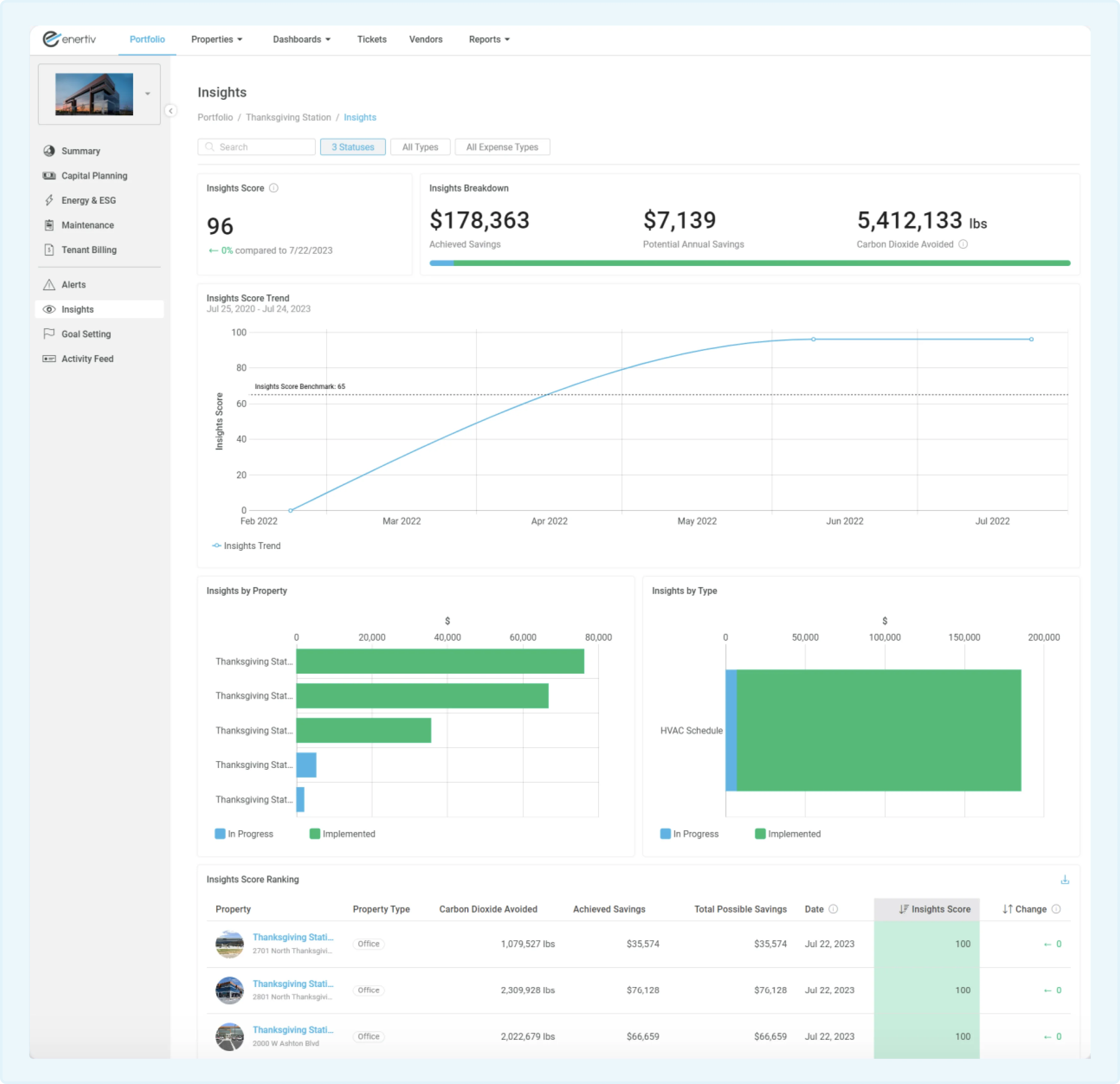
STEP 4 - FUTURE PROOFING
While all of this has been happening, the campus experienced significant turnover in on-site technicians.
Fernando recognized that the digital foundation created by Enertiv could also be used to speed up the ramp up time for new operators.
Usually, it takes around four months to fully train and onboard a new technician. With the Enertiv App, Fernando expects this time to be cut in half.
They will be able to see what’s been done in the property in the past and follow the best practice templates enshrined in Enertiv.
The time saved will not only benefit operators, Fernando will continue to be able to focus on performance instead of answering questions about where assets are located.