Are You Losing Money to this HVAC Mistake?
There are plenty of issues that can arise in HVAC systems in commercial real estate. In this video, Enertiv's Head of Client Success, Mark Pando, focuses on optimizing HVAC balance points, a common problem with an easy fix and large impact.
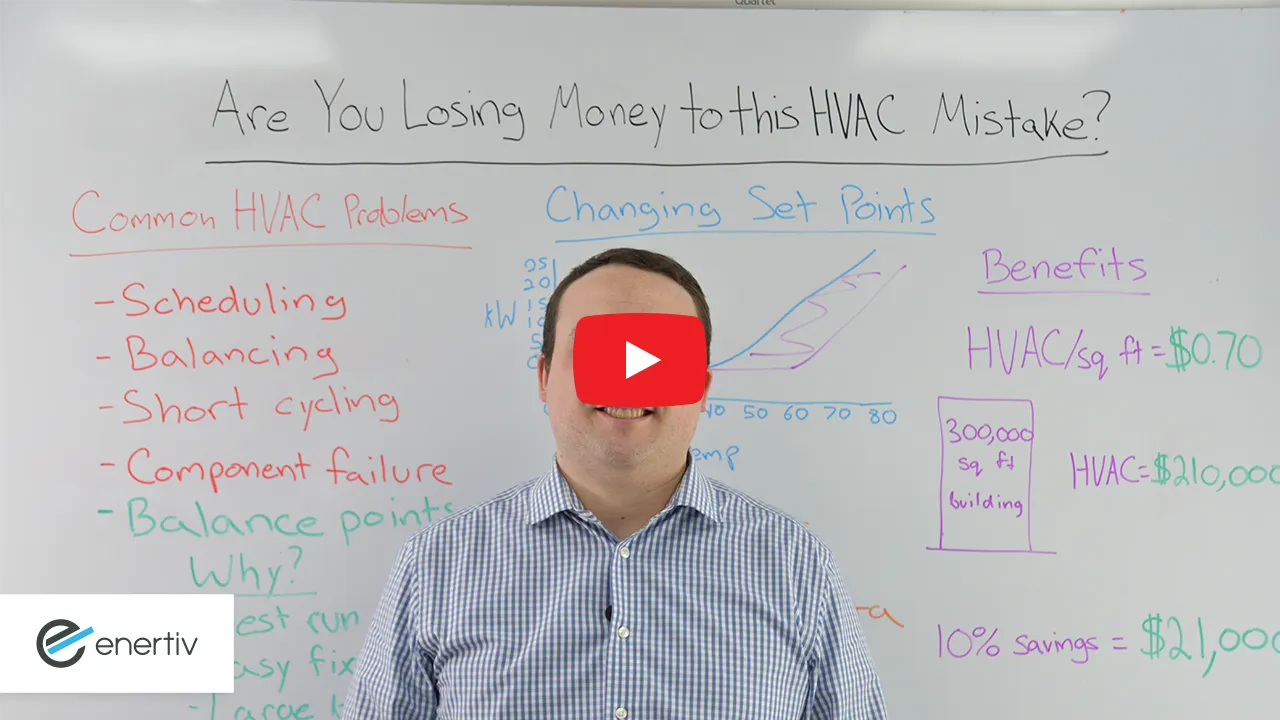
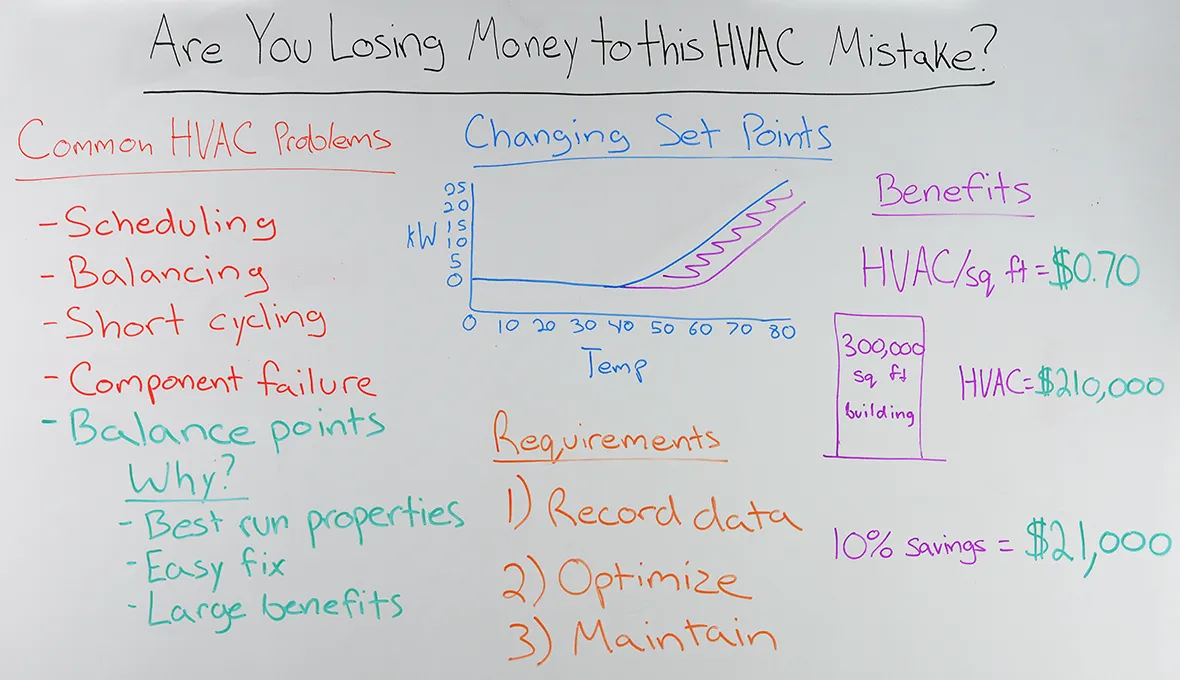
Video Transcription
Hi, my name is Mark Pando and I’m the head of client success here at Enertiv.
Today we’re going to talk about one way to optimize the performance of your HVAC systems.
We see all kinds of problems with HVAC systems in our client’s buildings. They range from scheduling problems, balancing issues, short cycling, component failure, and what we’re going to focus on today: balance points.
Why? There’s a few reasons. First of all, we see this in all kinds of real estate assets. We see this in some of the most well instrumented buildings, with robust centralized control systems. We also see this in totally uninstrumented buildings with no centralized control whatsoever.
Second, and most important, this is an easy fix. Changes can be made by your operators today to improve equipment performance without purchasing any equipment to save money tomorrow.
And last, but certainly not least. This is an impactful change that can deliver real, meaningful energy savings without purchasing any equipment.
Understanding Balance Points
So, what’s a balance point? A balance point is the temperate at which an HVAC system begins to operate. And what’s the problem with balance points? Often, we see HVAC systems are set up to operate when they don’t need to be, which is what we’re going to focus on now.
How do we go about investigating this and optimizing the performance of a system when it comes to the balance point? The first step is recording data. Hopefully you have access to real-time, equipment-level performance data to help you with this process. But it can also be done the old fashion way with engineers in the field filling out log books with daily temperatures, equipment operations, things like that. As long as you flip through those records, you can put together a picture like we have for this chiller.
Looking at this picture, we can see here that the balance point is 40 degrees. This chiller begins to operate right now at about 40 degrees based on the data we’ve collected. Moving to step 2 in the process, we need to optimize this system.
Does this chiller need to operate when it’s 40 degrees out? Most likely it doesn’t need to. The trick here is to push that balance point further along into warmer temperatures without compromising tenant comfort. If we can move this operating curve out to the right, to about 60 degrees, we can achieve all the energy savings represented here.
And the last step once you have optimized the system is to put some mechanisms in place to maintain those performance gains over time. The trick is to go back to step one and have some ongoing data recording, so you can catch exactly when this chiller begins to operate when it’s colder out. When it drifts back to turning on at 40 degrees, you have a way of identifying that right away and taking corrective action to move it back to its optimized state.
Benefits
So, what’s the impact of all of this? If we look at a typical commercial building, we’re looking at about 70 cents a square foot to operate the HVAC equipment in that asset. If we extend that to a 300,000 square foot commercial building, we’re looking at $210,000 a year just to operate the HVAC equipment.
If we can optimize the balance points across all the HVAC equipment in that building, and achieve 10% savings, we’re looking at $21,000 in energy savings that you can achieve today without purchasing any equipment.
You just have to put some mechanisms in place to record equipment performance, understand how it’s operating, optimize the performance of that asset to make sure it’s operating only when it needs to without (sacrificing tenant comfort). And finally, put some mechanisms in place to maintain that performance and catch when this piece of equipment drifts back towards its original, unoptimized condition.
I hope you enjoyed todays video, if you have any feedback, I’d love to hear it in the comments below. Thank you and have a great day.
IoT-based predictive maintenance can handle this process automatically for you. Schedule a demo today to see how.